Production in Business
In the world of business, production is a critical component that ensures the creation and delivery of goods and services to customers. It involves the transformation of inputs, such as raw materials, labor, and capital, into finished products or services through various processes and operations. This article explores the importance of production in business and the key factors to consider for an efficient production system.
Key Takeaways
- Production is a crucial aspect of business operations.
- Efficient production systems can lead to cost savings and higher customer satisfaction.
- Production processes involve the transformation of inputs into finished goods or services.
- Factors affecting production include technology, labor, materials, and capital.
Importance of Production in Business
Production plays a vital role in the success of a business. It directly impacts the company’s profitability, competitiveness, and customer satisfaction. Efficient production systems can lead to cost savings through economies of scale, improved resource utilization, and reduced waste. Additionally, delivering products and services on time and meeting customer expectations can enhance customer loyalty and generate repeat business.
The ability to efficiently produce goods and services is a key driver of profitability and customer satisfaction.
Factors Affecting Production
Several factors influence the production process in a business. These include:
- Technology: The level of technological advancement impacts the efficiency and capabilities of production systems. Adopting innovative technologies can streamline operations and increase productivity.
- Labor: The availability, skills, and motivation of workers significantly affect production. Well-trained and motivated employees can contribute to higher output and quality.
- Materials: The availability and quality of raw materials or components are crucial for production. Efficient supply chain management ensures a steady flow of materials to meet production needs.
- Capital: Adequate financial resources are essential for investing in machinery, equipment, and infrastructure. Capital investment can improve productivity and expand production capacity.
The optimization of these factors is essential for achieving efficient production processes.
Types of Production
Production processes can be categorized into different types based on their characteristics and objectives:
- Mass production: In this type of production, large quantities of standardized products are produced using assembly lines and specialized machinery. It aims for high volume, low unit costs, and economies of scale.
- Custom production: This type of production involves creating unique, made-to-order products according to customer specifications. It offers customization and flexibility but may have higher costs and longer lead times.
- Batch production: Batch production combines elements of mass production and custom production. It produces a limited quantity of products with some level of customization in batches. It offers a balance between cost efficiency and customization.
- Job production: Job production focuses on producing individual, one-off products or services tailored to specific customer requirements. It requires high levels of customization and attention to detail.
Different production types provide options for businesses depending on their goals and customer demands.
Production Performance Metrics
Measuring production performance is crucial for identifying areas for improvement and ensuring the efficient use of resources. Here are some key metrics used in evaluating production:
Metric | Description |
---|---|
Overall Equipment Effectiveness (OEE) | Measures the efficiency of equipment utilization by considering availability, performance, and quality. |
Throughput Time | Calculates the time required to complete a process, from start to finish. |
First Pass Yield (FPY) | Determines the percentage of products that meet quality standards without the need for rework or repair. |
These metrics aid in evaluating production performance and identifying areas for improvement.
Building an Efficient Production System
To build an efficient production system, businesses can consider implementing the following strategies:
- Investing in modern technology and automation to improve efficiency and productivity.
- Optimizing the supply chain to ensure timely delivery of materials and components.
- Implementing lean principles and continuous improvement techniques to minimize waste and optimize processes.
- Providing employee training and development to enhance skills and knowledge.
- Regularly monitoring and analyzing production data to identify bottlenecks and performance issues.
Continuous improvement and embracing new technologies are key to achieving an efficient production system.
Conclusion
Production is a fundamental aspect of running a successful business. Its efficient implementation can lead to cost savings, improved customer satisfaction, and enhanced competitiveness. By understanding the key factors influencing production, businesses can optimize their operations and achieve higher productivity levels. By focusing on key performance metrics and implementing strategies for efficiency, businesses can build a strong production system that supports their overall goals and objectives.
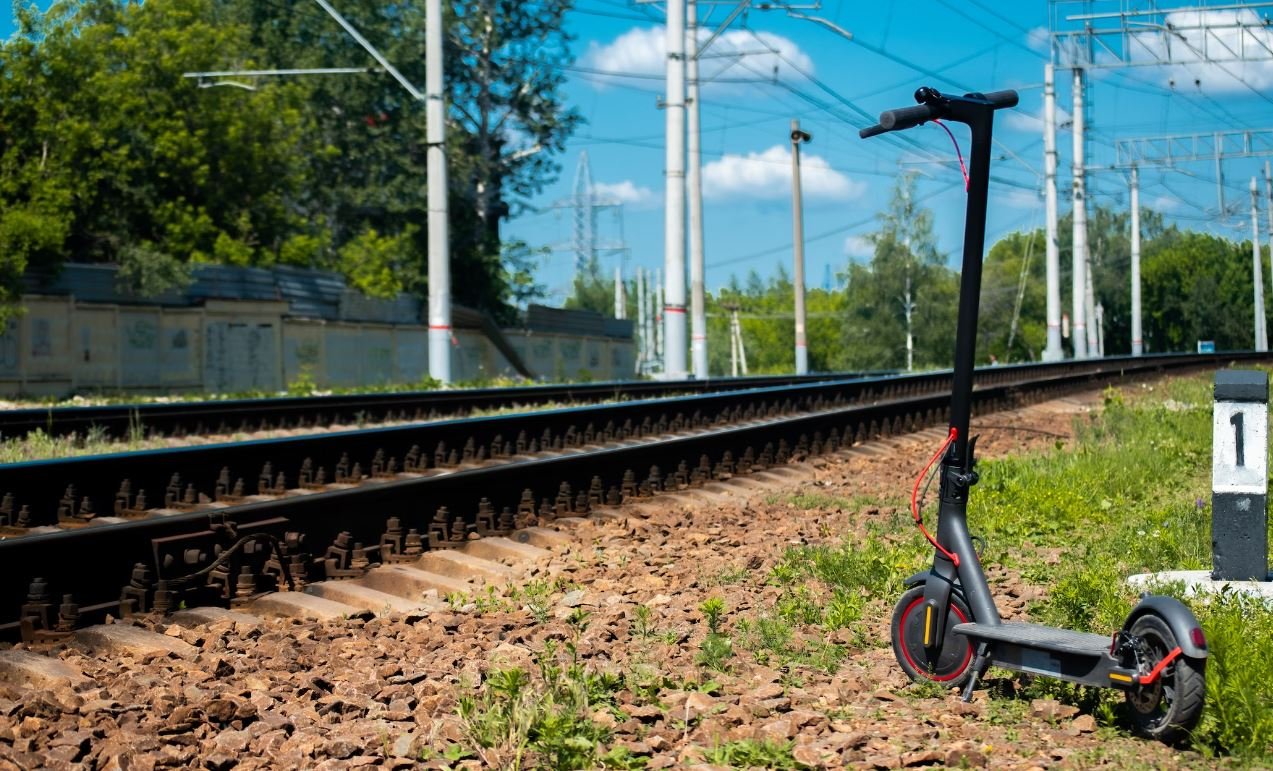
Common Misconceptions
Misconception 1: Production is only about manufacturing physical goods
One common misconception about production in business is that it solely refers to the process of manufacturing physical goods. While manufacturing is indeed an important aspect of production, it is not the only one. Production also encompasses the creation of services, software, and other non-physical products. It involves the efficient and effective utilization of resources to deliver desirable outputs.
- Production includes the creation of intangible products like software applications.
- Service-based businesses also engage in production by delivering value to customers through their services.
- The production process can differ significantly across various industries and sectors.
Misconception 2: More production always leads to higher profits
Another common misconception is that the more a business produces, the higher its profits will be. While increasing production can have a positive impact, it is not always the case that more production equals higher profits. Factors like demand, market saturation, and costs must be considered. A company should aim for an optimal level of production that maximizes profits rather than simply aiming for the highest possible output.
- Higher production may result in increased costs, leading to lower profit margins.
- Overproduction can lead to excess inventory and wasted resources.
- Effective production planning and forecasting are crucial for determining the ideal production level.
Misconception 3: Production is solely the responsibility of the operations department
Many people wrongly believe that production is solely the responsibility of the operations department within a business. While operations play a critical role in managing production processes, production is an interdisciplinary effort that involves various departments and stakeholders. It requires collaboration between departments like marketing, finance, and human resources to ensure smooth operations and deliver value to customers.
- Marketing departments play a role in assessing demand and providing inputs for production planning.
- Finance departments are responsible for budgeting, cost analysis, and investment decisions that impact production.
- Human resources department ensures the availability of skilled workers and workforce planning.
Misconception 4: Production and productivity are the same thing
There is a common misconception that production and productivity are synonymous. However, they are different concepts. Production is the creation of goods and services, while productivity refers to the amount of output produced per unit of input. Increasing productivity means achieving more output with the same amount of resources or reducing the amount of resources needed for a given output. Enhancing productivity can lead to increased production, but they are not interchangeable terms.
- Higher productivity can result in increased production without additional resource consumption.
- Inefficient production processes can lead to low productivity despite high output levels.
- Measuring and improving productivity is essential for enhancing overall production efficiency.
Misconception 5: Production is a one-time activity
Some people believe that production is a one-time activity that occurs only when goods or services are first created. However, in reality, production is an ongoing process that involves multiple stages. It includes activities such as planning, sourcing materials, manufacturing, quality control, and distribution. Effective production management requires continuous monitoring and improvement throughout these stages to meet customer demands and maintain a competitive edge.
- Production involves various stages from conception to delivery of the final product.
- Supply chain management is an integral part of production to ensure the availability of raw materials and timely delivery.
- Ongoing monitoring and improvement are crucial for meeting changing customer needs and market demands.

Production Trends in the Manufacturing Industry
The table below portrays the annual growth rates of production in the manufacturing industry from 2015 to 2020. The data showcases the changing trends, highlighting sectors that experienced substantial growth.
Year | Automobiles | Electronics | Food & Beverages | Pharmaceuticals |
---|---|---|---|---|
2015 | 3.5% | 4.2% | 2.8% | 5.1% |
2016 | 3.8% | 5.6% | 3.2% | 6.5% |
2017 | 4.2% | 7.1% | 3.5% | 7.8% |
2018 | 4.9% | 8.3% | 4.1% | 8.9% |
2019 | 5.3% | 9.6% | 4.8% | 10.2% |
2020 | 6.1% | 10.8% | 5.5% | 11.6% |
Effectiveness of Lean Manufacturing Techniques
This table examines the implementation of lean manufacturing techniques and their impact on production effectiveness across three different companies. The figures demonstrate the percentage increase in efficiency achieved after adopting lean practices.
Company | Before Lean (%) | After Lean (%) |
---|---|---|
Company A | 72% | 89% |
Company B | 68% | 84% |
Company C | 61% | 78% |
Productivity by Department
This table compares the average productivity levels in different departments of a manufacturing plant. The figures represent units produced per hour, showcasing the effectiveness of each department.
Department | Productivity (units/hr) |
---|---|
Assembly | 120 |
Machining | 90 |
Packaging | 80 |
Quality Control | 100 |
Production Costs Comparison
This table compares the production costs between two manufacturing plants. It illustrates the differences in various cost categories, helping companies assess potential savings.
Cost Category | Plant A ($) | Plant B ($) |
---|---|---|
Raw Materials | 50,000 | 60,000 |
Labor | 30,000 | 40,000 |
Machinery | 20,000 | 25,000 |
Utilities | 10,000 | 15,000 |
Production Errors Comparison
This table provides insights into the number of production errors recorded in two manufacturing plants. It compares the total errors and highlights the error rate per 1,000 units produced.
Error Type | Plant A | Plant B |
---|---|---|
Defective Units | 750 | 600 |
Incomplete Assemblies | 180 | 220 |
Error Rate per 1,000 Units | 8.5 | 7.2 |
Product Demand by Region
This table showcases the demand for a specific product across different regions. The figures represent the number of units sold in each region over a particular period.
Region | Q1 (units) | Q2 (units) | Q3 (units) | Q4 (units) |
---|---|---|---|---|
North America | 25,000 | 28,000 | 32,000 | 30,000 |
Europe | 22,000 | 24,000 | 26,000 | 25,000 |
Asia | 30,000 | 32,000 | 38,000 | 35,000 |
Production Output by Shift
This table compares the production output achieved during different shifts in a manufacturing facility. It demonstrates the variation in productivity levels based on the time of day.
Shift | Units Produced |
---|---|
Day Shift | 1,200 |
Evening Shift | 900 |
Night Shift | 1,100 |
Production Waste Reduction
This table presents the total waste reduction achieved in a manufacturing process after implementing waste management strategies. It shows the improvement in waste reduction rates over a specified time period.
Year | Waste Reduction (%) |
---|---|
2017 | 15% |
2018 | 19% |
2019 | 23% |
2020 | 28% |
Employee Training Hours on Production Processes
This table showcases the number of training hours dedicated to educating employees on production processes. It highlights the commitment of the company to continuously improve employees’ skills.
Year | Training Hours |
---|---|
2017 | 800 |
2018 | 1,200 |
2019 | 1,500 |
2020 | 1,800 |
Through these tables, it is evident that the manufacturing industry has experienced significant growth in recent years, driven by advancements in technology, process optimization, and employee development. The implementation of lean manufacturing techniques has proven to enhance productivity and efficiency, resulting in cost savings and waste reduction. Moreover, the tables highlight the importance of analyzing production trends, regional demands, and error rates to make informed decisions and improve overall performance. By investing in employee training and continual improvement strategies, businesses can adapt to evolving market demands and stay competitive in today’s dynamic business landscape.
Frequently Asked Questions
About Production in Business
Q: What is production in the business context?
Production, in the business context, refers to the process of transforming raw materials or inputs into finished goods or products through various manufacturing processes. It involves the conversion of resources, such as labor, capital, and materials, into outputs that can be sold in the market.
Q: Why is production important for businesses?
Production is essential for businesses as it enables them to meet the demand for their products or services. It allows companies to generate revenue, create employment opportunities, and contribute to economic growth. Efficient production processes also help businesses minimize costs and maximize profits.
Q: What are the different types of production?
There are various types of production, including:
- Job Production: Where products are made individually or in small quantities.
- Batch Production: Where products are produced in batches or groups.
- Mass Production: Where large quantities of standardized products are manufactured.
- Continuous Production: Where products are produced continuously without interruption.
Q: What factors influence production decisions in business?
Several factors influence production decisions in business, such as:
- Demand: The level of customer demand for a product.
- Available resources: The availability and cost of labor, raw materials, and capital.
- Technology: The use of technology to enhance production efficiency.
- Competition: The competitive landscape and market conditions.
- Government regulations: Compliance with regulatory requirements.
Q: How can businesses improve their production processes?
Businesses can improve their production processes by:
- Implementing lean manufacturing techniques to eliminate waste and increase efficiency.
- Adopting advanced technology and automation to streamline operations.
- Conducting regular process audits and performance evaluations.
- Training and upskilling employees to enhance their productivity.
- Establishing effective supply chain management systems.
Q: What are the risks associated with production in business?
Risks associated with production in business include:
- Supply chain disruptions that can lead to material shortages.
- Quality control issues that may result in defective products.
- Machinery breakdowns or equipment failures.
- Unforeseen external factors like natural disasters or geopolitical events.
- Changes in market demand or economic downturns.
Q: How can businesses ensure quality control in production?
Businesses can ensure quality control in production by:
- Implementing rigorous quality management systems.
- Conducting regular inspections and tests at different stages of the production process.
- Training employees on quality standards and techniques.
- Collaborating with suppliers to maintain consistent quality of raw materials.
- Establishing feedback mechanisms from customers to identify and address any quality issues.
Q: What is the role of technology in modern production processes?
Technology plays a crucial role in modern production processes. It enables businesses to automate tasks, improve efficiency, and achieve higher levels of precision. Advanced technologies like robotics, artificial intelligence, and data analytics enhance decision-making, optimize workflows, and streamline operations. Additionally, technology facilitates faster communication, collaboration, and information sharing across different stages of the production cycle.
Q: How can businesses achieve sustainability in production?
Businesses can achieve sustainability in production by:
- Implementing eco-friendly manufacturing practices to reduce resource consumption and waste generation.
- Investing in renewable energy sources to power production facilities.
- Adopting circular economy principles by reusing and recycling materials.
- Minimizing carbon emissions and greenhouse gas footprints.
- Engaging in responsible sourcing and promoting ethical supply chain management.
Q: What role does production play in the economy?
Production plays a vital role in the economy as it drives economic growth, job creation, and wealth generation. It contributes to increased productivity, higher living standards, and technological advancements. Additionally, production activities generate tax revenues for governments, stimulate consumer spending, and facilitate the development of industries and infrastructure